Cable tray grounding is an indispensable aspect of electrical installations that plays a pivotal role in ensuring safety, reliability, and efficiency. It involves connecting cable trays to the facility’s grounding system, providing a low-impedance path for fault currents and protecting personnel and equipment from electrical hazards. This comprehensive guide delves into the complexities of cable tray grounding, offering in-depth insights into its importance, principles, design considerations, installation best practices, and maintenance requirements.
The Importance of Cable Tray Grounding
Proper cable tray grounding serves several crucial purposes:
1. Enhanced safety: Grounding provides a safe path for fault currents to flow, significantly reducing the risk of electric shock to personnel and preventing damage to equipment due to overvoltage or insulation failure. It also safeguards against fire hazards caused by excessive heat generated during fault conditions.
2. Protection against lightning strikes: Grounding cable trays can help dissipate the energy from lightning strikes, safeguarding the electrical system and connected equipment from potential damage. By directing the lightning current to the ground, grounding minimizes the likelihood of voltage surges and transients that could harm sensitive electronic devices.
3. Minimization of electromagnetic interference (EMI): Grounding cable trays can minimize the generation and propagation of EMI, which can interfere with sensitive electronic equipment and communication systems. Proper grounding helps maintain signal integrity and ensures the smooth operation of data and communication networks.
4. Improved system reliability: By effectively managing fault currents and voltage surges, grounding contributes to the overall reliability and stability of the electrical system. It reduces the likelihood of equipment malfunctions, downtime, and repair costs, thereby enhancing the operational efficiency of the facility.
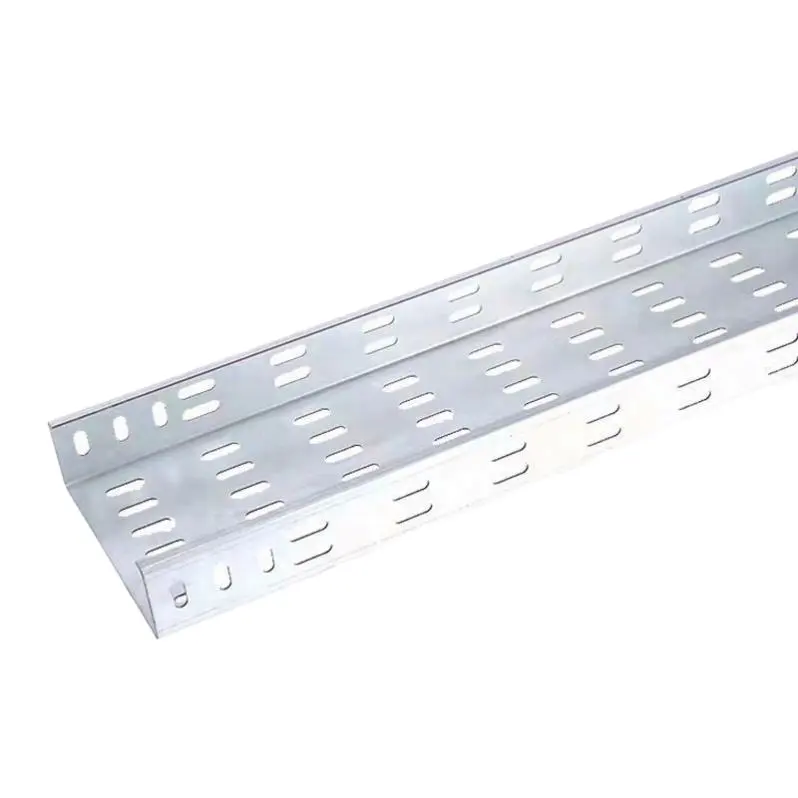
Fundamentals of Cable Tray Grounding
Effective cable tray grounding relies on the following fundamental principles:
1. Low-impedance path: The grounding system should provide a low-resistance path for fault currents to flow, ensuring rapid clearing of faults and minimizing hazardous voltage rises. A low-impedance path helps protect personnel from electric shock and prevents damage to electrical equipment.
2. Continuity: Grounding connections should be continuous and free from breaks or discontinuities, ensuring a reliable ground fault current path. Any interruption in the grounding path can lead to increased touch and step potentials, posing a risk to personnel and compromising the effectiveness of the grounding system.
3. Compatibility: Materials used for grounding components should be compatible with the cable tray system and the environment to prevent corrosion and ensure long-term performance. Compatibility also refers to the ability of grounding materials to withstand mechanical stress, temperature fluctuations, and other environmental factors.
4. Sizing and spacing: Grounding conductors should be appropriately sized and spaced to handle expected fault currents without overheating or sustaining damage. Sizing and spacing calculations should consider the maximum fault current, conductor material, and ambient temperature to ensure the grounding system can perform effectively under various fault conditions.
Design Factors for Cable Tray Grounding
When designing a cable tray grounding system, consider the following key factors:
1. Grounding electrode system: Determine the type and location of grounding electrodes based on local codes, soil conditions, and the facility’s specific requirements. Common grounding electrodes include ground rods, plates, water pipes, and concrete encased electrodes. The choice of electrode depends on factors such as soil resistivity, available space, and the magnitude of fault currents.
2. Grounding conductor size: Calculate the required size of grounding conductors using industry standards like NEC or IEC guidelines to ensure they can safely carry fault currents. Consider factors such as the maximum fault current, the distance between the cable tray and the grounding electrode, and the desired fault clearing time when determining conductor size.
3. Bonding jumpers: Implement bonding jumpers between adjacent cable trays, supports, and accessories to maintain a continuous ground fault current path and minimize touch and step potentials. Bonding jumpers should be made of suitable materials, properly sized, and securely fastened to ensure effective fault current dissipation.
4. Grounding connections: Ensure grounding connections are secure, accessible for inspection and maintenance, and made with appropriate connectors, clamps, or hardware. Connections should be corrosion-resistant and capable of handling the expected fault currents without overheating or sustaining damage.
5. Segregation of circuits: Separate grounding conductors for different voltage levels or circuit types to prevent cross-grounding and potential safety issues. Segregation helps avoid circulating ground currents and ensures that each circuit has a dedicated ground fault current path.
Installation Best Practices
Follow these guidelines for installing a robust and reliable cable tray grounding system:
1. Site preparation: Assess the installation site for obstacles or hazards and ensure supporting structures are suitable for grounding connections. Address any issues related to soil resistivity, proximity to other underground utilities, or environmental factors that may affect the grounding system’s performance.
2. Grounding conductor installation: Install grounding conductors according to industry standards and local codes, using approved methods and materials. Route grounding conductors in a protected manner to avoid physical damage or exposure to corrosive substances. Ensure that grounding conductors are adequately insulated and separated from power conductors to prevent accidental contact.
3. Bonding jumper installation: Install bonding jumpers between adjacent cable trays, supports, and accessories, ensuring they are securely fastened and provide a low-impedance path for fault currents. Use proper crimping, soldering, or welding techniques to create reliable connections between bonding jumpers and grounding conductors.
4. Grounding connections: Make sure grounding connections are tight and corrosion-resistant, using appropriate hardware and coatings to enhance conductivity and durability. Apply anti-corrosion treatments or use materials resistant to corrosion in harsh environments.
5. Testing and verification: Conduct continuity tests, insulation resistance tests, and ground fault current tests to verify the effectiveness of the grounding system and identify any potential issues. Perform these tests before energizing the electrical system and at regular intervals to ensure ongoing performance and compliance with industry standards.
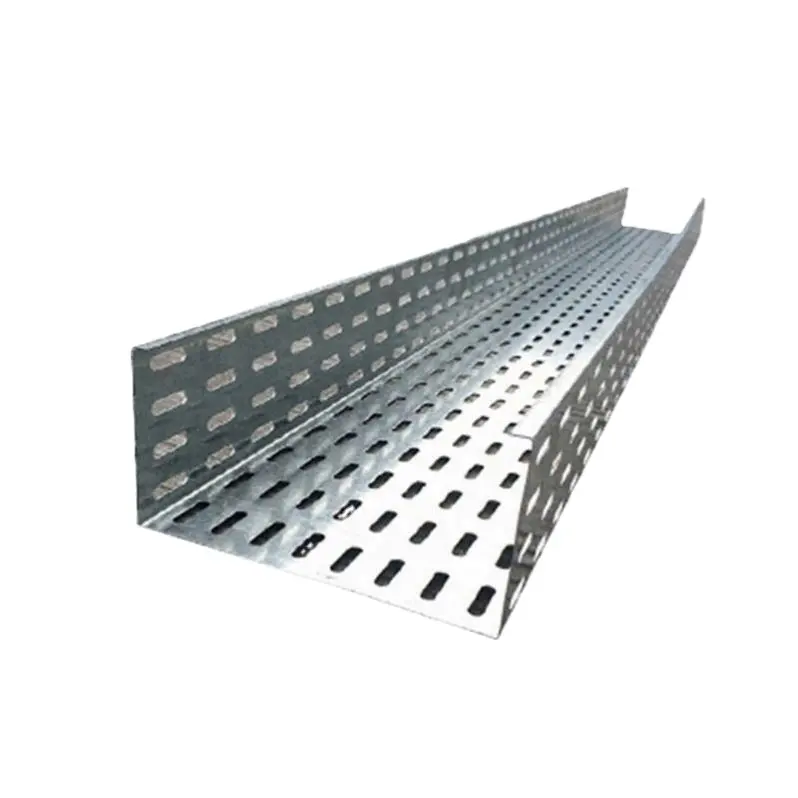
Maintenance and Testing
Regular maintenance and testing are vital for ensuring the ongoing effectiveness and safety of cable tray grounding systems:
1. Visual inspections: Conduct periodic visual inspections of grounding conductors, bonding jumpers, and connections to identify signs of damage, wear, or corrosion. Pay particular attention to exposed or buried sections of grounding conductors, as well as connections to grounding electrodes and cable trays.
2. Cleaning and corrosion prevention: Clean grounding components and apply protective coatings or treatments to prevent corrosion and maintain conductivity. Regular cleaning helps remove dirt, debris, and other contaminants that can impede the flow of fault currents.
3. Testing and measurement: Perform routine tests, such as earth resistance measurements, ground fault current tests, and ground impedance analysis, to assess the integrity and performance of the grounding system. These tests provide valuable insights into the grounding system’s ability to manage fault currents and protect personnel and equipment from electrical hazards.
4. Repair and replacement: Address defects, damages, or failures identified during inspections or testing promptly. Repair or replace grounding components as needed, using approved methods and materials. Document all maintenance activities and test results to demonstrate compliance with industry standards and local codes.
Conclusion
Cable tray grounding is an essential aspect of electrical installations that significantly impacts safety, reliability, and efficiency. By understanding the principles, design considerations, installation best practices, and maintenance requirements of cable tray grounding, you can ensure a robust and effective grounding system that protects personnel, equipment, and infrastructure. Stay vigilant in your efforts to maintain and improve your cable tray grounding system, and it will continue to serve your facility well for years to come.
Remember to consult relevant industry standards, local codes, and expert guidance to ensure compliance and optimal performance in your specific application. Regular training and education for personnel involved in the design, installation, and maintenance of cable tray grounding systems are also crucial for maintaining a safe and reliable electrical environment.