Cable tray ladder, often referred to as ladder-type cable tray, is a widely adopted and versatile system for managing and organizing electrical cables in various industrial, commercial, and institutional settings. This comprehensive guide delves into the intricacies of cable tray ladder systems, exploring their key features, applications, design considerations, installation best practices, and the reasons why they are indispensable components in modern electrical installations.
What is Cable Tray Ladder?
A cable tray ladder is an engineered cable management solution that consists of parallel side rails and equally spaced crossbars, resembling a ladder structure. The primary materials used for manufacturing cable tray ladders include galvanized steel, stainless steel, aluminum, and fiber-reinforced plastic (FRP). The side rails provide structural support, while the crossbars can be either solid or perforated, depending on the specific requirements of the application.
The main function of cable tray ladder is to provide a secure, organized, and accessible pathway for routing and supporting electrical cables, power lines, and communication cables. Cable tray ladders are designed with adaptability, safety, and efficiency in mind, enabling easy installation, maintenance, and expansion while accommodating varying cable sizes, types, and loads.
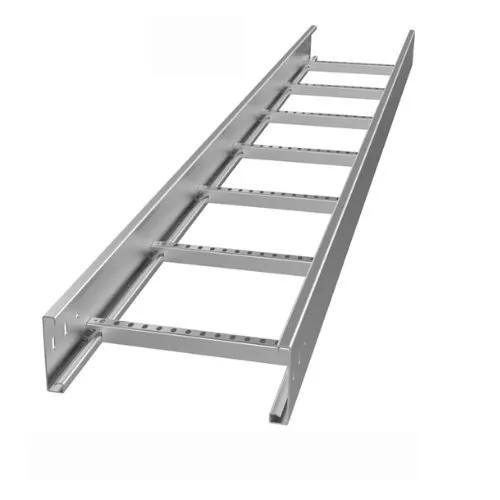
Why is Cable Tray Ladder Important?
Cable tray ladders play a critical role in ensuring safety, efficiency, and reliability in electrical installations. Several factors contribute to their importance:
1. Enhanced safety: Cable tray ladders help minimize electrical hazards by providing a designated route for cables, reducing the risk of accidental contact with personnel or other equipment. They also promote proper grounding and bonding, which is essential for protecting against electrical shocks, fires, and other potential dangers.
2. Improved organization and accessibility: Cable tray ladders offer a structured and easily accessible platform for cable management, simplifying the installation, modification, or replacement of cables as needed. This organized approach reduces clutter, facilitates faster troubleshooting and maintenance, and enhances overall system performance.
3. Flexibility and adaptability: Cable tray ladders are available in various materials, sizes, and configurations, allowing them to be customized for different applications and environments. Their modular design enables easy expansion or reconfiguration to accommodate changes in cable layouts or additional wiring requirements.
4. Cost-effectiveness: Cable tray ladders are generally more cost-effective than traditional conduit systems due to their ease of installation, reduced labor costs, and lower material expenses. Additionally, their open structure allows for better heat dissipation, which can extend the lifespan of cables and reduce replacement costs.
5. Compliance with regulations and standards: Cable tray ladders are designed to meet international standards and local codes, ensuring that electrical installations comply with safety and performance requirements. Compliance helps protect personnel, infrastructure, and equipment from potential risks and liabilities.
6. Aesthetics and cleanliness: Cable tray ladders contribute to a cleaner and more professional appearance in industrial and commercial settings by concealing cables and preventing unsightly cable spaghetti. This organized approach enhances workplace safety and visual appeal.
7. Environmental protection: Cable tray ladders can be designed with materials and finishes that offer resistance to corrosion, chemicals, and extreme temperatures, ensuring the longevity and integrity of the cable management system in challenging environments.
8. Fire resistance and smoke control: Specialized cable tray ladders can be manufactured with fire-resistant materials and coatings, providing additional protection against fire spread and minimizing the production of toxic smoke in case of a fire.
Design Considerations for Cable Tray Ladder Systems
When designing a cable tray ladder system, consider the following key factors:
1. Load capacity: Determine the maximum load that the cable tray ladder will need to support, taking into account the weight of cables, environmental factors, and any future expansion plans.
2. Cable fill ratio: Ensure compliance with industry standards and guidelines regarding the maximum allowable cable fill percentage within the cable tray ladder to prevent overcrowding and maintain proper airflow.
3. Cable tray size and configuration: Select the appropriate size and configuration of the cable tray ladder based on the number and size of cables, required bend radius, and available space.
4. Material selection: Choose the most suitable material for the cable tray ladder based on factors such as environment, corrosion resistance, mechanical strength, and cost.
5. Access and support requirements: Plan for adequate access points, support structures, and mounting hardware to facilitate installation, maintenance, and cable routing.
6. Grounding and bonding: Implement a robust grounding and bonding strategy to ensure the safe dissipation of fault currents and minimize the risk of electrical hazards.
7. Compatibility with other system components: Ensure that the cable tray ladder is compatible with existing electrical infrastructure, including raceways, conduits, junction boxes, and cable connectors.
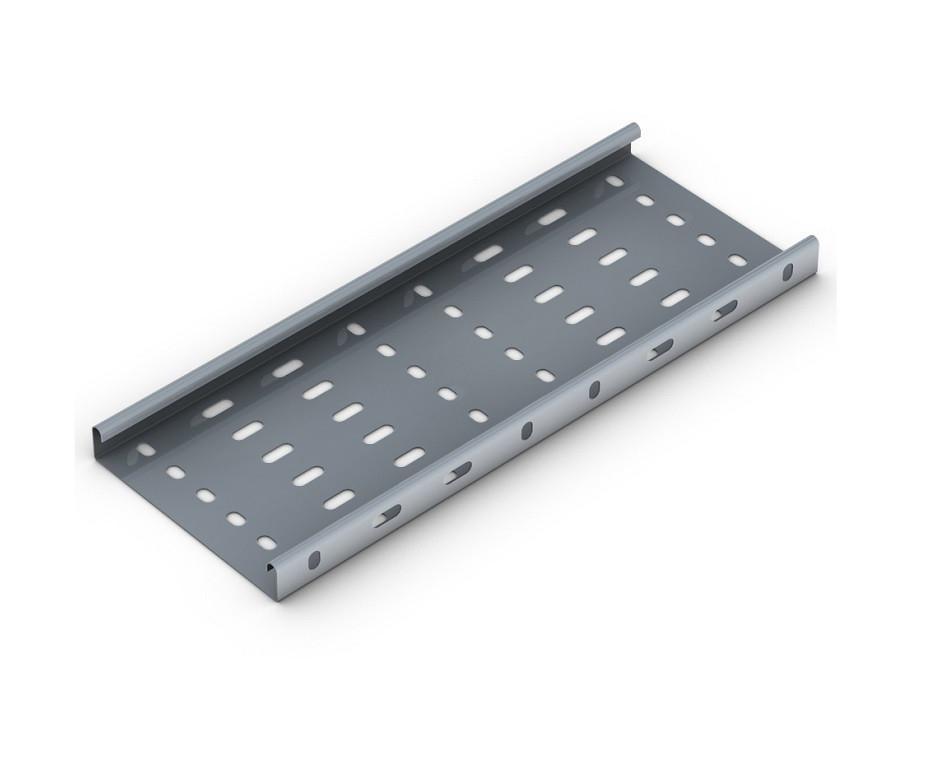
Installation Best Practices for Cable Tray Ladder Systems
Follow these guidelines for installing a robust and reliable cable tray ladder system:
1. Site preparation: Assess the installation site for obstacles, structural limitations, and environmental factors that may impact the cable tray ladder’s performance and longevity.
2. Layout planning: Develop a detailed layout plan, considering cable routes, support locations, and clearance requirements to ensure compliance with industry standards and local codes.
3. Support structure inspection: Verify the integrity and suitability of support structures, such as walls, beams, or columns, for mounting the cable tray ladder.
4. Cutting and drilling: Precisely cut and drill the cable tray ladder components according to the layout plan, using appropriate tools and techniques to minimize damage and ensure a secure fit.
5. Assembly and mounting: Assemble the cable tray ladder sections, supports, and accessories, following manufacturer instructions and industry best practices. Securely mount the assembled cable tray ladder to the designated support structures.
6. Cable installation: Install cables in the cable tray ladder according to the established cable fill ratio, maintaining proper bend radius and separation between cables to prevent damage and ensure efficient heat dissipation.
7. Grounding and bonding: Connect the cable tray ladder to the facility’s grounding system, ensuring low-impedance paths for fault currents and complying with relevant standards and guidelines.
8. Insulation and protection: Apply appropriate insulation and protective coatings or covers to cables and cable tray ladder components, as needed, to safeguard against environmental factors, mechanical damage, or electrical hazards.
Maintenance and Testing of Cable Tray Ladder Systems
Regular maintenance and testing are vital for ensuring the ongoing effectiveness and safety of cable tray ladder systems:
1. Visual inspections: Conduct periodic visual inspections of the cable tray ladder, cables, and connections to identify signs of damage, wear, or corrosion.
2. Cleaning and corrosion prevention: Clean cable tray ladders and apply protective coatings or treatments to prevent corrosion and maintain conductivity. Regular cleaning helps remove dirt, debris, and other contaminants that can impede the flow of fault currents or compromise cable integrity.
3. Cable condition assessment: Monitor the condition of cables within the cable tray ladder, checking for signs of damage, aging, or overheating. Replace or repair damaged cables as necessary.
4. Testing and measurement: Perform routine tests, such as continuity tests, insulation resistance tests, and ground fault current tests, to verify the integrity and performance of the cable tray ladder system and identify any potential issues.
5. Documentation and recordkeeping: Maintain accurate records of inspections, tests, repairs, and replacements performed on the cable tray ladder system, ensuring compliance with industry standards and local codes.
Applications of Cable Tray Ladder
Cable tray ladders find widespread use in a variety of industries and applications, including:
1. Industrial facilities: Manufacturing plants, warehouses, and processing centers rely on cable tray ladders to manage power and control cables for machinery, automation systems, and lighting.
2. Commercial buildings: Office complexes, retail stores, and hotels employ cable tray ladders to organize data and communication cables, as well as power cables for HVAC, lighting, and other building services.
3. Healthcare facilities: Hospitals, clinics, and research institutions utilize cable tray ladders to support critical electrical systems, such as life-saving medical equipment, emergency power supplies, and advanced communication networks.
4. Educational institutions: Schools, universities, and research labs use cable tray ladders to manage power and data cables for classrooms, laboratories, and administrative areas.
5. Data centers and IT facilities: Cable tray ladders play a vital role in maintaining the structural integrity and organization of complex cabling infrastructures in data centers, server rooms, and network facilities.
6. Transportation infrastructure: Airports, railway stations, and ports employ cable tray ladders to manage power and communication cables for lighting, signaling, and control systems.
7. Outdoor applications: Cable tray ladders are suitable for outdoor installations, such as utility substations, telecommunications towers, and solar or wind energy farms, where they provide protection against environmental factors and ensure reliable cable management.
8. Hazardous locations: Cable tray ladders can be designed and certified for use in hazardous locations, such as explosion-proof or intrinsically safe areas, ensuring compliance with stringent safety requirements.
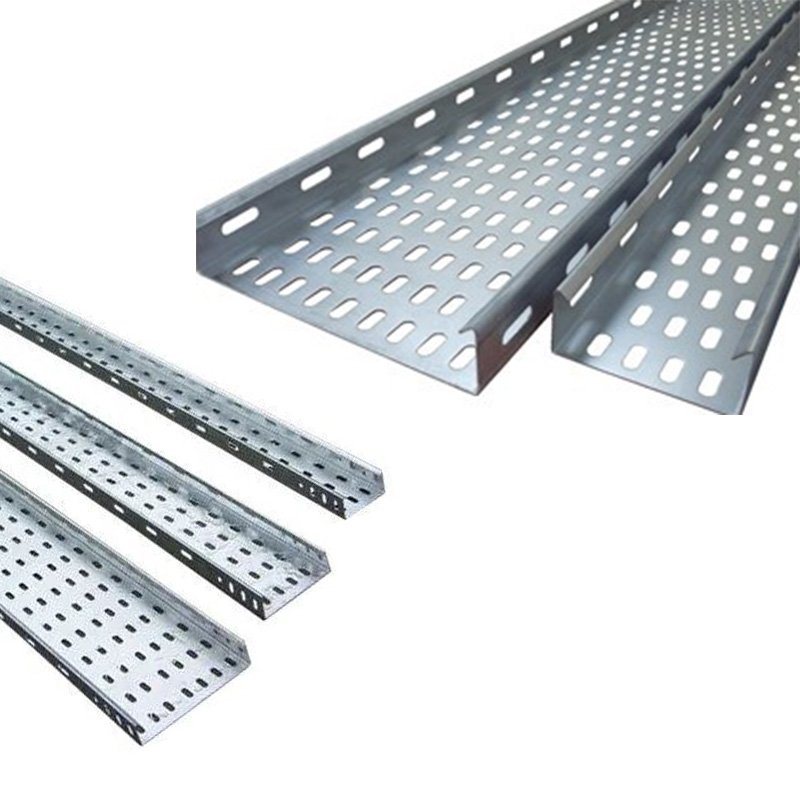
Conclusion
Cable tray ladders are indispensable components in modern electrical installations due to their numerous benefits, including enhanced safety, improved organization, flexibility, cost-effectiveness, compliance with regulations, aesthetic appeal, and environmental protection. By understanding the importance and applications of cable tray ladders, engineers, facility managers, and contractors can make informed decisions when designing and implementing cable management solutions for various industrial, commercial, and institutional settings.
Stay vigilant in your efforts to adhere to industry standards, local codes, and best practices when designing, installing, and maintaining cable tray ladder systems. Regular training and education for personnel involved in cable management projects are crucial for maintaining a safe and reliable electrical environment. With careful planning, execution, and ongoing maintenance, cable tray ladders will continue to serve as a cornerstone of efficient and secure cable management in a wide range of applications.